-
Laijing Bu
Hi there! Welcome to my shop. Let me know if you have any questions.
Your message has exceeded the limit.

The transformation process of austenite during heat treatment
2025-07-17 11:05:53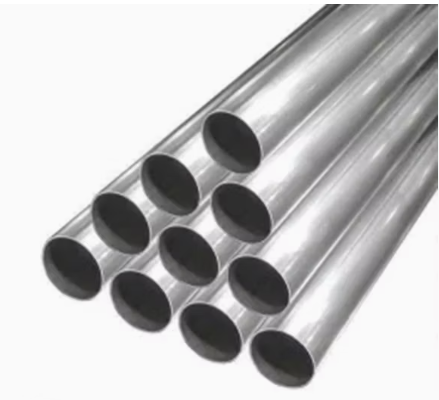
During the heat treatment process, the transformation of austenite (γ-Fe, face-centered cubic structure, a solid solution of carbon in γ-Fe) is the core step that determines the final microstructure and properties of steel materials. It mainly consists of two stages: the formation of austenite (austenitization) and the cooling transformation of austenite. The following is a detailed description of the transformation process and its characteristics:
I. Formation of Austenite (Austenitization)
Austenitization refers to the process where steel is heated above its critical temperature (Ac₁ or Ac₃), and pearlite (a mixture of ferrite and cementite) transforms into austenite. Its essence is the transformation of the crystal structure from body-centered cubic (ferrite) to face-centered cubic (austenite) through atomic diffusion. It is divided into four stages:
1. Austenite nucleation
When heated above the Ac₁ temperature, austenite first nucleates at the interface between ferrite and cementite in pearlite. This is because the interface has high energy (existence of distortion energy) and the carbon concentration is uneven (the carbon content in ferrite is low, while that in cementite is high), meeting the thermodynamic and kinetic conditions for nucleation.
2. Austenite growth
The nucleated austenite crystals continue to grow by "absorbing" ferrite and cementite from the surrounding area:
Ferrite (body-centered cubic) transforms into austenite (face-centered cubic) through atomic rearrangement;
Cementite (Fe₃C) decomposes into carbon and iron atoms, and carbon atoms diffuse into the austenite (the solubility of carbon in austenite is much higher than that in ferrite).
3. Residual carbide dissolution
When pearlite completely transforms into austenite, if the heating temperature is high enough or the holding time is long enough, the incompletely decomposed cementite (residual carbides) will continue to dissolve into the austenite until it disappears completely.
4. Austenite composition homogenization
Due to the uneven carbon concentration distribution in the initial austenite (higher carbon content in the cementite area and lower in the ferrite area), composition homogenization through the diffusion of carbon atoms is required, ultimately forming a compositionally uniform austenite.
II. Cooling Transformation of Austenite
The cooling transformation of austenite is a key aspect in heat treatment (the core of processes such as quenching, annealing, and normalizing), and the transformation products depend on the cooling rate and transformation temperature. It can be divided into two main categories: isothermal transformation (transformation at a constant temperature) and continuous cooling transformation (transformation during continuous cooling). Corresponding to different transformation products.
1. Isothermal Transformation (Based on TTT Curve)
Isothermal transformation refers to rapidly cooling austenite to a certain temperature (below A₁) and holding it at that temperature to complete the transformation under constant temperature conditions. The transformation law can be described by the TTT curve (isothermal transformation kinetics curve). Depending on the transformation temperature, the products can be classified into three types:
(1) Pearlite Transformation (High Temperature Zone, A₁ to 550°C)
Transformation mechanism: Diffusion-type transformation (both iron atoms and carbon atoms undergo diffusion).
Product form: A layered mixture of ferrite (α-Fe) and cementite (Fe₃C), known as pearlite.
Based on the degree of refinement of the lamellar spacing, it can be classified as:
Pearlite: The lamellar spacing is relatively coarse (spacing > 0.5 μm), easily distinguishable under an optical microscope;
Spheroidite: The lamellar spacing is relatively fine (0.1 - 0.5 μm), requiring high-power microscopy observation;
Triclinite: The lamellar spacing is extremely fine (<0.1 μm), only distinguishable through electron microscopy.
Performance characteristics: The finer the lamellar spacing, the higher the strength and hardness (such as triclinite hardness > spheroidite > pearlite), but the toughness is generally good.
(2) Bainite Transformation (Medium Temperature Zone, 550°C to Ms Point)
Transformation mechanism: Semi-diffusion-type transformation (iron atoms do not diffuse, while carbon atoms undergo short-distance diffusion).
Product form: According to the formation temperature, it can be classified as:
Upper Bainite: Formed in the range of 550°C to 350°C, presenting a "feather-like" appearance (parallel arrangement of ferrite strips, with carbonitrides distributed between the strips);
Lower Bainite: Formed in the range of 350°C to the Ms point, presenting a "needle-like" appearance (uniformly distributed fine carbonitride particles within ferrite needles).
Performance characteristics: Upper Bainite has poor toughness (the interstrip carbonitrides are prone to causing stress concentration); Lower Bainite has high strength (hardness 50 - 60 HRC) and good toughness (better than upper Bainite and pearlite), being an excellent composite material structure.
(3) Martensite Transformation (Low Temperature Zone, below the Ms Point)
Transformation mechanism: Non-diffusion-type transformation (atoms only undergo shear displacement, without long-distance diffusion), belonging to "shear-type" transformation.
Product form: Over-saturated carbon α-Fe solid solution (body-centered cubic structure), presenting needle-like or plate-like forms:
High-carbon Martensite: When the carbon content is > 1.0%, it presents "needle-like" (intersecting and with microscopic cracks);
Low-carbon Martensite: When the carbon content is <0.2%, it presents "plate-like" (parallel arrangement, without cracks).
Performance characteristics: The hardness is extremely high (low-carbon martensite ~ 30 - 50 HRC, high-carbon martensite ~ 60 - 65 HRC), but brittle (especially high-carbon martensite), and after transformation, there will be residual austenite (residual austenite).
Critical temperatures:
Ms Point: The starting temperature of martensite transformation (decreases with increasing carbon content, pure iron Ms ≈ 910°C, with 1.0% carbon, Ms ≈ 210°C);
Mf Point: The ending temperature of martensite transformation (with excessive carbon content, Mf may be lower than room temperature, resulting in residual austenite at room temperature). The cooling rate is relatively slow (such as normalizing): Under air cooling conditions, fine lamellar pearlite (Scheelite) is obtained;
The cooling rate is relatively fast (such as oil cooling): It may result in bainite (medium-speed cooling);
The cooling rate is extremely fast (such as water quenching): Beyond the "critical cooling speed", it is directly overcooled below the Ms point, resulting in martensite (+ residual austenite).
III. Key Factors Affecting Austenite Transformation
1. Chemical Composition:
Carbon content: Increasing the carbon content will lower the Ms and Mf points, increase the amount of residual austenite; accelerate the pearlite transformation and delay the bainite and martensite transformations.
Alloy elements: Elements such as Cr, Ni, and Mn lower the Ms point and delay the martensite transformation; elements such as Si and Mo refine the pearlite or bainite structure.
2. Austenitization Conditions:
The higher the heating temperature and the longer the holding time, the coarser the austenite grains, the more uniform the composition, and the slower the subsequent cooling transformation rate (coarse grains reduce the nucleation rate).
Cooling speed: It is the core factor determining the transformation products (for example, the key to quenching is "rapid cooling to avoid the pearlite / bainite transformation zone").
Summary
Tags: austenite steel