-
Laijing Bu
Hi there! Welcome to my shop. Let me know if you have any questions.
Your message has exceeded the limit.

What is the optimal ratio of each element in austenitic stainless steel pipes?
2025-07-15 09:52:50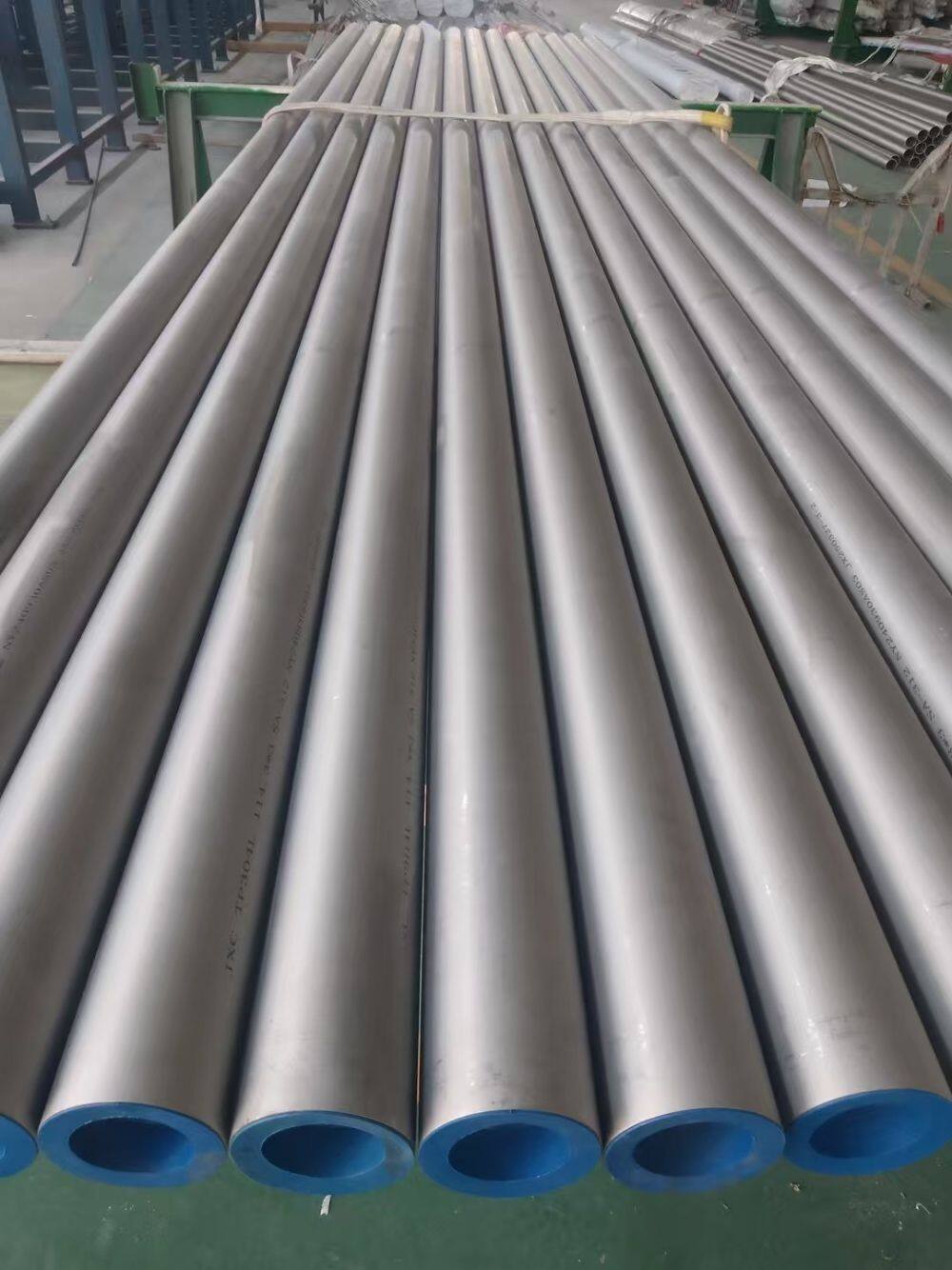
The performance of austenitic stainless steel pipes mainly depends on the synergistic effect of elements such as chromium (Cr) and nickel (Ni), and the element ratios of different grades vary due to requirements such as corrosion resistance and strength. The following is an analysis of the optimal elemental ratios, functions, and application scenarios for typical austenitic stainless steel pipes:
1、 Universal austenitic stainless steel (304/304L series)
Core features: Balancing corrosion resistance and cost-effectiveness, non-magnetic, suitable for conventional corrosive environments.
Picture 1
2、 Corrosion resistant enhanced austenitic stainless steel (316/316L series)
Core feature: Adding molybdenum (Mo) significantly improves the resistance to pitting and crevice corrosion, making it suitable for chloride containing ions or strongly corrosive media.
Picture 2
3、 High temperature stable austenitic stainless steel (321/347 series)
Core feature: Adding titanium (Ti) or niobium (Nb) to prevent intergranular corrosion caused by carbide precipitation at high temperatures, suitable for high-temperature working conditions.
Picture 3
4、 High manganese low nickel austenitic stainless steel (200 series, such as 201/202)
Core feature: Using manganese (Mn) to replace some nickel, with low cost but poor corrosion resistance, suitable for scenarios with low corrosion resistance requirements.
Picture 4
5、 Special purpose austenitic stainless steel (such as 310S, 904L)
1. 310S (high temperature resistant type)
Element ratio: Cr 24-26%, Ni 19-22%, C ≤ 0.08%.
Function: With high chromium nickel content, it still has excellent oxidation resistance at 1000-1200 ℃ and is used for furnace tubes and heat treatment equipment.
2. 904L (Super Austenitic Stainless Steel)
Element ratio: Cr 19-23%, Ni 23-25%, Mo 4-5%, C ≤ 0.02%.
Function: Resistant to strong corrosive media such as sulfuric acid and phosphoric acid, used in petrochemical and hydrometallurgy industries.
Summary of the synergistic effects of key elements
Cr Ni synergy: Cr forms a passive film, Ni stabilizes austenite and enhances corrosion resistance, and the ratio of the two is usually maintained at 2:1 to 3:1 (such as Cr ≈ 18-20% and Ni ≈ 8-10% in 304).
Corrosion resistance enhancement of Mo: In media containing Cl ⁻, SO ₄² ⁻, etc., Mo can improve the repair ability of passivation films. The Mo content in the 316 series should be ≥ 2%.
Control of C: Prioritize low-carbon grades (such as 304L/316L) in welding scenarios to avoid intergranular corrosion; High temperature scenarios rely on Ti/Nb fixed carbon (such as 321/347).
Application selection suggestions
Conventional corrosion-resistant scenario: choose 304/304L, with high cost-effectiveness;
Chlorine containing ions or seawater environment: choose 316/316L (Mo ≥ 2%);
High temperature welded parts: Choose 321 (Ti stable) or 347 (Nb stable);
Low cost non critical scenario: Option 201, but attention should be paid to corrosion resistance limitations.
The specific ratio can refer to national standards (such as GB/T 24511) or ASTM A240. In practical applications, it needs to be adjusted based on the composition of the medium, temperature, pressure, and other working conditions.
Tags: Universal austenitic stainless steel (304/304L series), Corrosion resistant enhanced austenitic stainless steel (316/316L series), Special purpose austenitic stainless steel (such as 310S, 904L)