-
Laijing Bu
Hi there! Welcome to my shop. Let me know if you have any questions.
Your message has exceeded the limit.

Introduction to degreased stainless steel welded pipes
2025-07-15 14:24:41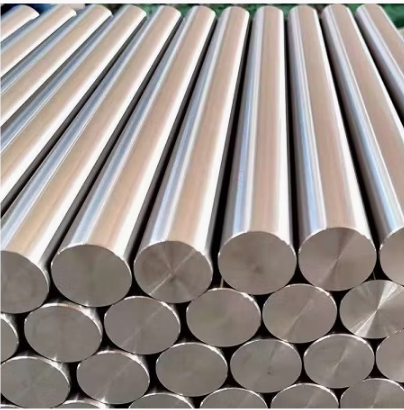
I. The Core Function of Degreasing Process
1. Cleaning the Surface
The purpose of degreasing is to remove contaminants such as grease, lubricants, and metal debris from the surface of stainless steel welding pipes. This process typically involves pre-cleaning, chemical degreasing (using alkaline solutions or environmentally friendly biodegradable agents), high-pressure rinsing, and drying. For precision applications, ultrasonic or plasma degreasing techniques can be used to ensure extremely high cleanliness of both the inner and outer surfaces of the pipes.
2. Improving Welding Quality
Degreasing before welding can prevent the decomposition of grease at high temperatures, which may cause pores or inclusions, ensuring the tightness and strength of the weld seam. Degreasing after welding is used to remove residual flux from the welding process, preventing corrosion risks.
3. Protecting the Passivation Layer
A proper degreasing process does not damage the passivation layer (the chromium-rich oxide layer) on the surface of stainless steel. Instead, it creates conditions for subsequent passivation treatment, further enhancing corrosion resistance.
II. Performance Characteristics and Industry Standards
1. Material and Structural Advantages
The use of 304, 316L, and other austenitic stainless steels ensures excellent corrosion resistance, high-temperature oxidation resistance, and mechanical strength. The welds undergo solution treatment and on-line eddy current testing to ensure no defects, making them suitable for high-pressure and high-purity environments.
2. Surface Quality Requirements
According to standards such as ASTM A270, ISO 2037, and GB/T 12771, the pipes after degreasing must pass surface tension tests (≥32 mN/m), visual inspections, and particle count tests to ensure no visible contaminants and no residual chemicals.
3. Sanitary Design
The design of the inner wall roughness (Ra ≤ 0.8 μm) and the smooth transition of welds (without depressions or protrusions) meet the requirements of the food and pharmaceutical industry for microbial control and can be used in CIP (Continuous In-Line Cleaning) and SIP (Continuous In-Line Sterilization) systems.
III. Typical Application Domains
1. Food and Beverage Industry
The pipelines used for liquid foods such as dairy products, beer, and fruit juices are designed to ensure product integrity and prevent contamination. For example, the pipelines in aseptic filling lines must undergo strict degreasing and passivation to comply with FDA and EU 10/2011 regulations.
2. Pharmaceuticals and Biopharmaceuticals
The pipelines for pharmaceutical equipment, bioreactors, and infusion systems are made of degreased stainless steel welded pipes to prevent the adsorption or degradation of active pharmaceutical ingredients. Some high-end applications also require the inner walls of the pipes to be electro-polished (Ra ≤ 0.2 μm).
3. Chemicals and Environmental Protection
When transporting corrosive media (such as acid and alkali solutions), 316L degreased welded pipes perform exceptionally well. In environmental protection equipment, high-cleanliness pipeline systems can be used to handle wastewater and exhaust gases.
4. Semiconductor and Electronics
The transportation of ultra-pure water and high-purity gases requires stainless steel pipes that have undergone electro-degreasing and electron beam welding to meet the strict particle and metal ion content limits set by SEMI standards.
IV. Market Status and Technological Trends
1. Major Producers
Domestic enterprises such as Jiulitiecai and Qingshan Steel Pipe, as well as international brands like Japan's JFE and Germany's ThyssenKrupp, all have large-scale production capabilities and offer a full range of products from industrial grade to sanitary grade.
2. Demand Growth Drivers
With stricter global food and drug safety regulations and the expansion of the semiconductor industry, the decontaminated stainless steel pipe market continues to grow. The global market size has exceeded 8 billion US dollars in 2024, and it is expected to have a compound annual growth rate of 6.5% in the next five years.
3. Technological Innovation Directions
Environmental-friendly processes: The application of biodegradable decontaminants and low-temperature plasma cleaning technology reduces chemical pollution.
Intelligent detection: Integration of laser scanning and AI visual detection systems enables real-time identification of surface defects.
Customized services: Provide customized production with pipe diameters (6-600mm), wall thicknesses (0.5-10mm), and special surface treatments (such as matte, mirror finish) according to customer requirements.
V. Suggestions for Selection and Usage
1. Select the material based on the medium
For general corrosive environments, 304 stainless steel can be chosen. In severe corrosive scenarios, 316L or duplex stainless steel (such as 2205) should be used.
2. Pay attention to the processing method
3. Verify cleanliness
Require the supplier to provide a degreasing treatment report and a third-party inspection certificate to ensure compliance with the hygiene standards of the target industry.
Degreased stainless steel pipe, with its precise manufacturing process and strict quality control, has become an indispensable key component in the high-end industrial field. With the continuous advancement of technology, its application prospects in emerging fields such as new energy and high-end manufacturing will also be broader.
Tags: Some interesting facts about deoxidized stainless steel