Home > Blog > Will the degreasing treatment of the deoxidized stainless steel pipe affect its performance?
-
Laijing Bu
Hi there! Welcome to my shop. Let me know if you have any questions.
Your message has exceeded the limit.

Will the degreasing treatment of the deoxidized stainless steel pipe affect its performance?
2025-07-15 14:21:46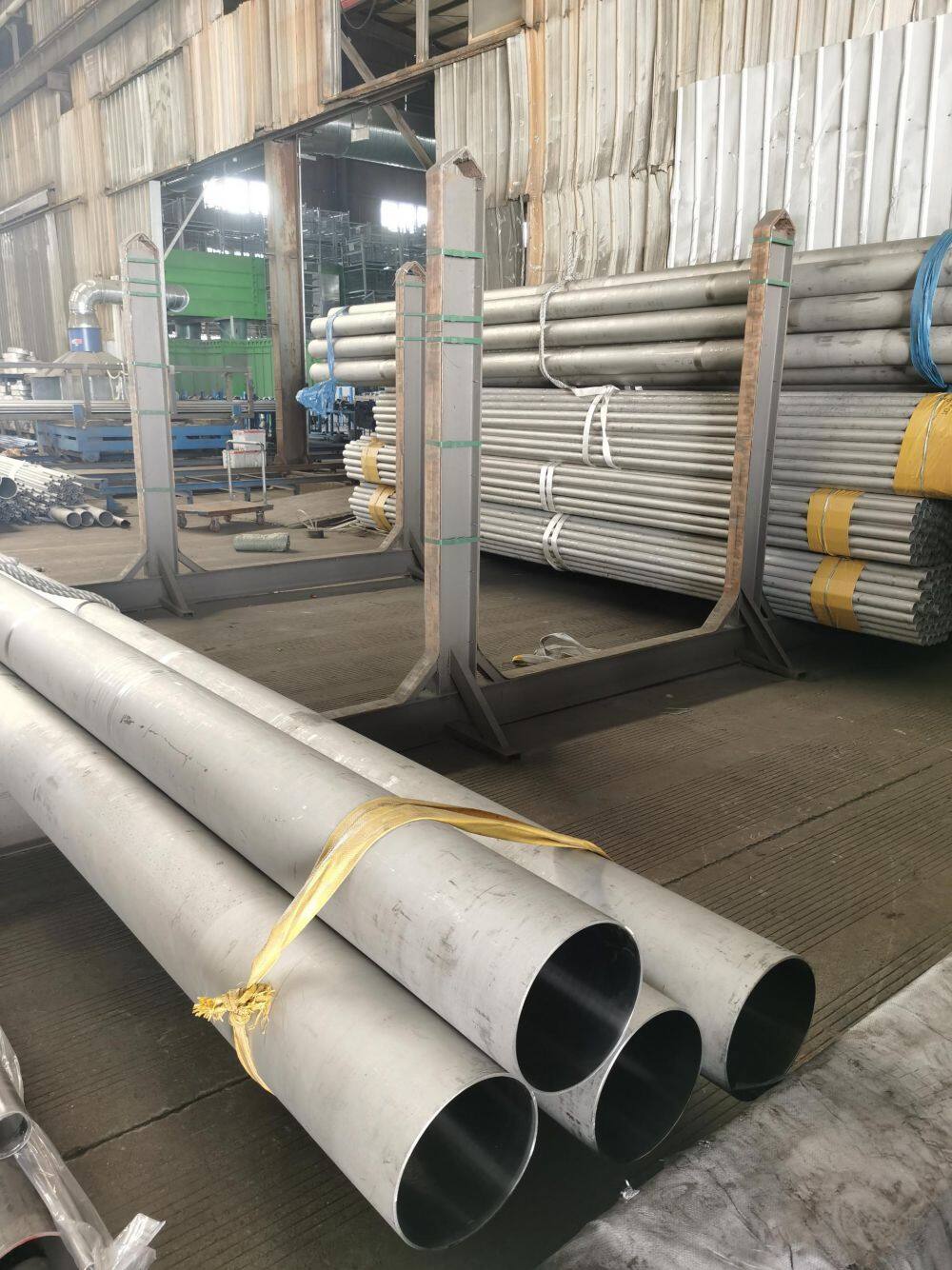
The degreasing treatment of deoxidized stainless steel pipes generally does not have a negative impact on their core performance. On the contrary, a proper degreasing process can enhance their safety and reliability during use. The following provides an analysis from the perspectives of the purpose of degreasing, the principle of the process, and the specific effects on performance:
I. Purification Purpose and Process Principles
1. Core Purpose of Decontamination
During the production process of stainless steel welded pipes (such as rolling, welding, storage, and transportation), the surface may still have impurities like grease, lubricants, oil stains, or metal debris. The main purpose of decontamination is:
Removing contaminants: To prevent the formation of an isolation layer by grease during subsequent processing (such as acid washing, passivation), which would affect the surface treatment effect;
Meeting hygiene or corrosion resistance requirements: Especially in industries such as food, medicine, and chemicals, residual grease may contaminate the medium or accelerate local corrosion. Decontamination is a crucial step to ensure that the products meet industry standards.
2. Common Decontamination Processes
Chemical Decontamination: Using alkaline solutions (such as sodium hydroxide, sodium carbonate) or solvents (acetone, ethanol) to dissolve grease, and removing oil stains through saponification reactions or similar compatibility principles;
Electrode Decontamination: Applying an electric current to the chemical decontamination solution, using electrolysis-generated bubbles to remove surface grease, which is more efficient;
Ultrasonic Decontamination: Combining ultrasonic vibration to accelerate the removal of grease, suitable for complex structure pipe fittings.
II. Specific Effects of Degreasing Treatment on the Properties of Stainless Steel Pipes
1. Impact on Mechanical Properties (Strength, Toughness, etc.)
No significant effect: The degreasing treatment mainly acts on the surface of the pipe (with a thickness of only a few micrometers to several tens of micrometers), while the mechanical properties of stainless steel are determined by the base material and internal structure (such as austenitic or ferritic structure).
Process safety: Reasonable control of degreasing temperature (usually ≤ 80℃) and time (a few minutes to several tens of minutes) will not cause changes in the base material structure or grain coarsening, so the indicators such as tensile strength, yield strength, elongation, etc. will not be affected.
2. Impact on Corrosion Resistance
Main positive effect:
Residual grease may form a "pitting corrosion" environment (where grease comes into contact with air and medium is prone to accumulate electrolytes), after degreasing, the surface becomes cleaner, reducing the risk of local corrosion;
Degreasing is often used as a pre-treatment step before passivation, removing oil stains, after which the passivation film (Cr₂O₃) can cover the surface more uniformly, improving the overall corrosion resistance.
Notes: If the degreasing agent residue (such as alkaline solutions not thoroughly cleaned) remains, it may cause electrochemical corrosion in a humid environment, so it is necessary to ensure that the subsequent water washing or neutralization steps are complete.
3. Impact on Surface Quality and Function
Surface finish: After degreasing, there is no grease residue on the surface, the surface finish improves, especially suitable for scenarios requiring mirror polishing or coatings;
Hygiene performance: In food-grade and medical-grade applications, degreasing is a key to meeting the "no residue, easy cleaning" requirements, avoiding grease becoming a breeding ground for bacteria;
Welding compatibility: If the welded pipe needs to be re-welded, the surface grease will cause weld porosity, cracks, etc., after degreasing, the welding quality can be improved.
III. Risks Affecting Performance and Control Measures
1. Potential Risks
Overcorrosion: If the degreasing agent concentration is too high or the treatment time is too long, it may cause "over-corrosion" on the stainless steel surface, destroying the passivation film and reducing the corrosion resistance;
Stress Corrosion: During electro-degreasing, if the current density is inappropriate, additional stress may be introduced, increasing the risk of stress corrosion cracking in specific media (such as an environment with chloride ions).
2. Control Measures
Process Standardization: Select appropriate degreasing agent formulations and process parameters (such as temperature, time, and concentration) based on the pipe material (such as 304, 316L) and thickness;
Post-treatment Cleaning: Thoroughly rinse after degreasing with deionized water, and perform neutralization treatment (such as using dilute nitric acid to neutralize alkaline residues) if necessary;
Quality Inspection: Ensure the degreasing effect through visual inspection (no oil spots on the surface), continuous water film testing (uniform water adhesion without breakage), or grease residue detection (such as infrared spectroscopy analysis).
IV. Industry Application and Standard Requirements
Application Scenarios: Degreased stainless steel welded pipes are widely used in food and beverage pipelines, pharmaceutical equipment, chemical corrosion-resistant pipelines, high-purity gas transportation, etc. They must comply with industry standards such as FDA, 3A, and GMP;
Standard Requirements: For example, food-grade pipelines require that the oil residue be ≤ 50mg/m², while pharmaceutical-grade may require ≤ 10mg/m². The degreasing treatment must pass third-party testing and certification.
Summary
Decontamination treatment is an essential process for enhancing the surface cleanliness of stainless steel welded pipes and meeting high hygiene or corrosion resistance requirements. A standardized decontamination procedure will not compromise the mechanical properties and corrosion resistance of the pipes; instead, it can optimize their performance. The key lies in controlling the decontamination process parameters to avoid over-processing or residue. Quality can be ensured through subsequent cleaning and testing. If there are concerns about specific materials or application scenarios, industry standards (such as ASTM A269, GB/T 12771) or consulting with suppliers for process verification data can be referred to.
Tags: De-greasing of stainless steel