Home > Blog > How to ensure the service life of stainless steel pipes in medical laboratory gas pipelines?
-
Laijing Bu
Hi there! Welcome to my shop. Let me know if you have any questions.
Your message has exceeded the limit.

How to ensure the service life of stainless steel pipes in medical laboratory gas pipelines?
2025-07-18 13:22:24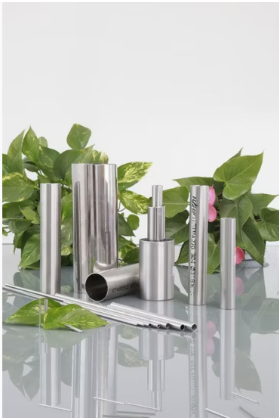
In medical laboratory gas pipeline systems, the service life of stainless steel pipes is influenced by multiple factors such as material selection, processing techniques, installation quality, and daily maintenance. From a full-cycle management perspective, the following key measures are provided to ensure a long service life:
I. Source Control: Material and Processing Technology Optimization
1. Strict Material Selection and Certification
Give priority to 316L stainless steel (containing Mo element, resistant to chloride ion corrosion). When transporting high-purity gases or corrosive gases, avoid using 304L (with slightly weaker corrosion resistance). Require suppliers to provide intergranular corrosion test reports (such as ASTM A262 E method) and chemical composition analysis certificates, ensuring carbon content ≤ 0.03%, sulfur and phosphorus content ≤ 0.03%, and eliminating the use of inferior recycled materials.
2. High-Precision Surface Treatment
The inner wall should be treated with electro-polishing (EP) instead of mechanical polishing, with a surface roughness Ra ≤ 0.4 μm (≤ 0.2 μm for high-purity gas pipelines), reducing the adsorption of impurities and bacterial growth in the gas.
After polishing, perform nitric acid passivation treatment to form a 5-10 nm thick Cr₂O₃ passivation film, and verify the passivation effect through the blue dot test (no blue dots indicate complete passivation).
3. Cleanliness Control Before Delivery
Pipes must undergo ultrasonic degreasing cleaning (solvent: ethanol or acetone), and be purged with high-purity nitrogen (purity ≥ 99.99%) until no visible particles are present on the inner wall.
Packaging should use vacuum sealing + moisture-proof paper to prevent dust and moisture from contaminating the inner wall during transportation.
II. Installation: Eliminating Human-induced Damage and Hazards
1. Standardized Welding Process
Automatic TIG track welding is adopted, with pure argon gas (flow rate 5-10L/min) filled inside the pipe during welding to protect the inner wall from oxidation and blackening (the oxide layer will accelerate corrosion). Each weld seam must undergo 100% helium mass spectrometry leak testing (leakage rate ≤ 1×10⁻¹⁰ Pa·m³/s) and X-ray inspection to eliminate false welding, pores and other defects.
2. Anti-corrosion Measures for Installation Details
Stainless steel is used for pipe supports. When in contact with carbon steel supports, PTFE isolation gaskets should be added to prevent electrochemical corrosion. The installation slope should be controlled at 0.5% to 1%. Stainless steel drain valves should be installed at the concentrated condensate water areas to prevent long-term retention of acidic condensate water (such as CO₂ dissolved in water to form carbonic acid) from corroding the inner wall.
3. Special Treatment for Oxygen Pipes
All pipes and valves in contact with oxygen must pass degreasing certification (no oil stains when wiped with white silk cloth). Tools containing grease are prohibited for installation to avoid explosion risks and damage to the passivation film.
III. Operation and Maintenance: Dynamic Monitoring and Preventive Maintenance
1. Regular Leak Detection
Use a helium mass spectrometer to inspect welds and joints every quarter, with a focus on stress concentration areas such as valves, elbows, and tees. For oxygen pipelines, use the soapy water method to check for leaks monthly. Mark and repair any bubbles immediately.
2. Gas Purity and Corrosive Medium Monitoring
Monitor the dew point (≤ -40℃) and oxygen content (≤ 1ppm) of high-purity gases (such as N₂, Ar) online to prevent rusting of the inner walls due to moisture and oxygen. When transporting corrosive gases (such as Cl₂, SO₂), install corrosion sensors at the end of the pipeline to monitor gas concentration in real time. Activate the exhaust system when the concentration exceeds the limit.
3. Inner Wall Cleaning and Passivation Repair
Use high-purity nitrogen (with 0.1% nitric acid solution) for circulation purging and passivation annually to repair minor damage to the passivation film. If rust spots are found on the inner wall of the pipeline, disassemble it and re-electrolyze and polish + passivate. Replace the pipeline section if the damage is severe.
IV. Environmental and System Design Optimization
1. Laboratory Environment Control
Maintain the laboratory humidity at ≤60% RH to prevent condensation on the outer walls of pipes. If there is acid mist (such as from hydrochloric acid evaporation), enhance ventilation or apply a corrosion-resistant coating (such as Teflon) to the outer walls of the pipes.
2. System Redundancy and Segmented Control
For critical gas pipelines (such as medical oxygen), design a dual backup system to facilitate switching during single-line maintenance. Install shut-off valves according to functional areas to isolate and repair damaged local pipelines without shutting down the entire system.
3. Anti-static and Grounding Design
When transporting flammable gases (such as H₂), ground the pipes every 100 meters (with a grounding resistance of ≤4Ω), and use copper braided straps to cross-connect flange joints to prevent static electricity accumulation and breakdown of the passivation film.
V. Targeted Measures for Special Gases
VI. Standardized Management and Personnel Training
1. Establish a Full Lifecycle Archive
Record the material batch number, welding date, inspection report, and maintenance record of each section of pipeline. Implement traceability management through QR code identification.
Formulate life assessment standards based on GB 50751 "Technical Code for Medical Gas Engineering". Pipelines over 15 years old need to undergo comprehensive flaw detection.
2. Operator Training
Prohibit overpressure operation (working pressure ≤ 80% of design pressure). Regularly train on emergency handling of pipeline leakage (such as using special tape for temporary sealing).
Maintenance personnel must master stainless steel surface repair techniques (such as the use of local electrolytic polishing equipment) to avoid secondary damage caused by non-professional operations.
Summary
The service life of stainless steel pipes in medical laboratories (typically 10-15 years) must be controlled throughout the entire chain of "material - process - installation - maintenance": based on high-purity corrosion-resistant materials, combined with high-precision surface treatment and defect-free welding, along with environment-adaptive design and dynamic monitoring, to ultimately achieve long-term system operation with low maintenance costs. For critical medical gases (such as oxygen and nitrous oxide), it is recommended to commission a third-party organization for comprehensive non-destructive testing + material aging assessment every five years, and replace potential risk sections in advance.
#Knowledge about Stainless Steel Seamless Tubes# #Knowledge about Stainless Steel Tubes# #Stainless Steel [Super Topic]# #Stainless Steel Precision Tubes# #Stainless Steel Tubes for Medical Oxygen Pipelines#
Tags: stainless steel pipes, medical laboratory gas pipeline