Home > Blog > Will the degreasing treatment of degreased stainless steel welded pipes affect their performance?
-
Laijing Bu
Hi there! Welcome to my shop. Let me know if you have any questions.
Your message has exceeded the limit.

Will the degreasing treatment of degreased stainless steel welded pipes affect their performance?
2025-07-15 10:07:39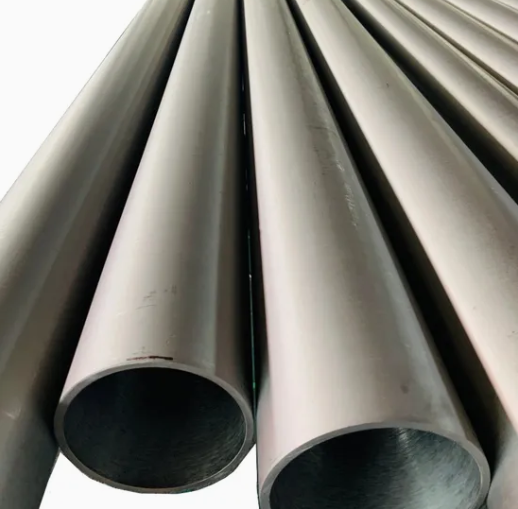
The degreasing treatment of degreased stainless steel welded pipes usually does not have a negative impact on their core performance. On the contrary, a reasonable degreasing process can improve their safety and reliability in use. The following analysis will focus on the purpose, process principle, and specific impact on performance of degreasing treatment:
1、 The purpose and process principle of degreasing treatment
1. The core purpose of degreasing
Stainless steel welded pipes may have residual impurities such as grease, lubricants, oil stains, or metal debris on the surface during production processes such as rolling, welding, and storage. The main purpose of degreasing treatment is to:
Remove pollutants: Avoid the formation of isolation layers of oil and grease during subsequent processing (such as acid washing and passivation), which may affect the surface treatment effect;
Meeting hygiene or corrosion resistance requirements: Especially in industries such as food, medicine, and chemical, oil residues may contaminate the medium or accelerate local corrosion. Defatting is a key step in ensuring that products meet industry standards.
2. Common degreasing processes
Chemical degreasing: using alkaline solutions (such as sodium hydroxide, sodium carbonate) or solvents (acetone, ethanol) to dissolve oil and remove oil stains through saponification reaction or similar solubility principle;
Electrolytic degreasing: Applying current to a chemical degreasing solution to remove surface oil and grease through bubbles generated by electrolysis, resulting in higher efficiency;
Ultrasonic degreasing: Combined with ultrasonic vibration to accelerate oil detachment, suitable for complex structural pipe fittings.
2、 The specific effect of degreasing treatment on the performance of stainless steel welded pipes
1. Impact on mechanical properties (strength, toughness, etc.)
No significant impact: The degreasing treatment mainly acts on the surface of the pipe (with a thickness of only a few micrometers to tens of micrometers), while the mechanical properties of stainless steel are determined by the matrix material and internal structure (such as austenite and ferrite structure).
Process safety: Reasonably control the degreasing temperature (usually ≤ 80 ℃) and time (several minutes to tens of minutes), which will not cause changes in the matrix structure or coarse grains, so the tensile strength, yield strength, elongation and other indicators are not affected.
2. Impact on corrosion resistance performance
The main positive effect is:
Residual oil and grease may form a "crevice corrosion" environment (where oil and grease come into contact with air or media and tend to accumulate electrolytes), resulting in a cleaner surface after degreasing and reducing the risk of localized corrosion;
Defatting is often used as a pre-treatment step before passivation. After removing oil stains, the passivation film (Cr ₂ O3) can cover the surface more evenly, improving the overall corrosion resistance.
Caution: If degreaser residue (such as alkaline solution not thoroughly cleaned), it may cause electrochemical corrosion in humid environments, so it is necessary to ensure that subsequent water washing or neutralization steps are in place.
3. Impact on surface quality and functionality
Surface smoothness: After degreasing, there is no oil residue on the surface, and the smoothness is improved, especially suitable for scenes that require mirror polishing or coating;
Hygiene performance: In food grade and medical grade applications, defatting is the key to meeting the requirements of "no residue, easy to clean", avoiding oil from becoming a breeding ground for bacteria;
Welding compatibility: If welded pipes require secondary welding, surface grease can cause defects such as porosity and cracks in the weld seam. Degreasing can improve welding quality.
3、 Risks and control measures that may affect performance
1. Potential risks
Excessive corrosion: If the concentration of degreaser is too high or the treatment time is too long, it may cause "excessive corrosion" on the surface of stainless steel, damage the passivation film, and instead reduce the corrosion resistance;
Stress corrosion: Improper current density during the electrolytic degreasing process may introduce additional stress, increasing the risk of stress corrosion cracking in specific media such as chloride ion environments.
2. Control measures
Process standardization: Select the appropriate degreasing agent formula and process parameters (such as temperature, time, concentration) based on the pipe material (such as 304, 316L) and thickness;
Post treatment cleaning: After degreasing, rinse thoroughly with deionized water and perform neutralization treatment if necessary (such as neutralizing alkaline residues with dilute nitric acid);
Quality inspection: The degreasing effect is ensured through visual inspection (no oil stains on the surface), water film continuity testing (even adhesion of water without breakage), or residual oil detection (such as infrared spectroscopy analysis).
4、 Industry applications and standard requirements
Application scenarios: Degreasing stainless steel welded pipes are widely used in food and beverage pipelines, pharmaceutical equipment, chemical corrosion-resistant pipelines, high-purity gas transportation and other fields, and must comply with industry standards such as FDA, 3A, GMP, etc;
Standard requirements: For example, food grade pipelines require a residual oil content of ≤ 50mg/m ², pharmaceutical grade pipelines may require a residual oil content of ≤ 10mg/m ², and degreasing treatment requires third-party testing and certification.
summarize
Degreasing treatment is a necessary process for stainless steel welded pipes to improve surface cleanliness, meet high hygiene or corrosion resistance requirements. Standardized degreasing processes will not damage the mechanical properties and corrosion resistance of the pipes, but can optimize their performance. The key is to control the degreasing process parameters, avoid excessive processing or residue, and ensure quality through subsequent cleaning and testing. If you have doubts about specific materials or application scenarios, you can refer to industry standards (such as ASTM A269, GB/T 12771) or consult suppliers to obtain process validation data.
Tags: The purpose and process principle of degreasing treatment, The specific effect of degreasing treatment on the performance of stainless steel welded pipes, Risks and control measures that may affect performance