Home > Blog > What are the requirements for degreased stainless steel pipes in medical oxygen pipelines
-
Laijing Bu
Hi there! Welcome to my shop. Let me know if you have any questions.
Your message has exceeded the limit.

What are the requirements for degreased stainless steel pipes in medical oxygen pipelines
2025-07-15 09:13:42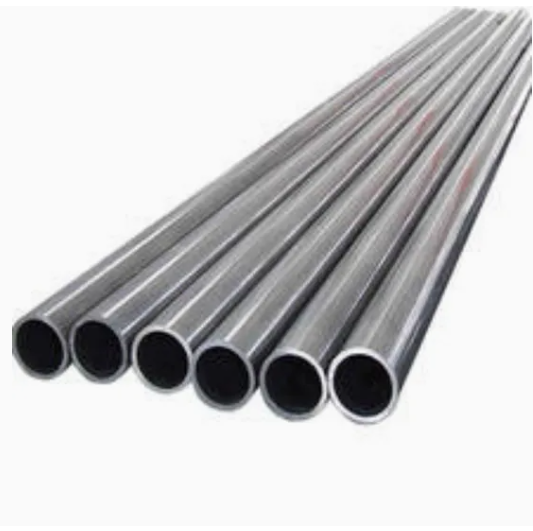
Medical oxygen pipelines have extremely strict requirements for degreased stainless steel pipes, which must meet safety, cleanliness, corrosion resistance, and medical standards at the same time. The specific requirements are as follows:
1、 Material and specification requirements
1. Material standards
Priority should be given to using 316L stainless steel (containing molybdenum, with stronger corrosion resistance) or 304L stainless steel to avoid intergranular corrosion during welding caused by high carbon content in ordinary 304 stainless steel.
The material must comply with medical grade standards, such as ASTM A270 (medical grade stainless steel pipes) in the United States and GB/T 14976 (seamless stainless steel pipes for fluid transport) in China, to ensure no heavy metal precipitation.
2. Specification requirements
The diameter of the pipe is designed according to the oxygen demand of the hospital (commonly DN15-DN100), and the wall thickness needs to meet the pressure requirements (usually working pressure of 0.2-0.8MPa), and the inner wall should be smooth (roughness Ra ≤ 0.8 μ m) to reduce oxygen flow resistance and impurity deposition.
2、 Degreasing treatment standard
1. Degreasing process requirements
Degreasing method: Use solvent degreasing (such as industrial alcohol, trichloroethylene) or alkaline degreasing. It is strictly prohibited to use chlorine containing solvents (which may corrode stainless steel or residual harmful substances).
Degreasing process
Pre treatment: Remove visible oil stains, welding slag and other impurities on the surface;
Soak or cycle clean the degreasing agent to ensure that the inner wall of the pipeline is completely in contact with the degreasing agent;
Rinse with high-pressure pure water (conductivity ≤ 10 μ S/cm) to remove residual degreaser;
Drying treatment: Blow with high-purity nitrogen gas (purity ≥ 99.99%) to prevent residual moisture from breeding microorganisms.
2. Cleanliness testing
Residual oil content: It needs to be detected by UV lamp (no fluorescent reaction of oil on the surface) or weight method (residual content ≤ 50mg/m ²).
Particle pollutants: Visual inspection or particle counter detection is used to ensure that there are no visible particles (≥ 5 μ m particles ≤ 10 particles/L) on the inner wall of the pipeline.
3、 Safety and pressure resistance requirements
1. Pressure and leakage testing
Pressure test: A water pressure test (1.5 times the working pressure, such as testing 1.2MPa for 0.8MPa pipelines) is required, and the pressure should be maintained for 30 minutes without leakage; The air pressure test (1.15 times the working pressure) requires high-purity nitrogen to prevent oil mist pollution in the air.
Airtightness test: Helium mass spectrometry leak detection is used, with a leakage rate of ≤ 1 × 10 ⁻⁹ Pa · m ³/s, to avoid safety hazards caused by oxygen leakage (which may explode in case of open flames).
2. Anti static and grounding
The pipeline needs to be grounded with static electricity throughout the entire process (grounding resistance ≤ 10 Ω) to prevent static sparks caused by high-speed oxygen flow, and to ensure charge conductivity with flange bridging (conductive gasket).
4、 Installation and welding requirements
1. Welding process
Automatic rail welding (TIG welding) is adopted to avoid the generation of welding slag and oxide scale during manual welding. During welding, high-purity argon gas (purity ≥ 99.99%) is filled inside the pipe for protection to prevent oxidation of the weld seam (the oxide layer may fall off and pollute the oxygen).
The weld seam needs to undergo acid pickling and passivation treatment to remove the surface oxide film, enhance corrosion resistance, and the weld seam roughness Ra ≤ 1.6 μ m.
2. Installation environment control
The installation process should be carried out in a clean environment (such as a clean workshop or temporary dust shed), and operators should wear dust-free clothing. Tools should be degreased and cleaned to avoid secondary pollution.
The pipeline support should be made of stainless steel material to prevent carbon steel support from rusting and contaminating the pipeline, and a PTFE gasket should be used to isolate the support from the pipeline to prevent electrochemical corrosion.
5、 Hygiene and certification requirements
1. Microbial control
After degreasing, the pipeline needs to undergo microbiological testing (such as bacterial colony count ≤ 100CFU/m ²) to avoid bacterial growth that may affect the purity of medical oxygen.
2. Industry certification
It is required to pass ISO 13485 (Quality Management System for Medical Devices), GMP (Good Manufacturing Practice) certification, and some countries also need to comply with FDA (US Food and Drug Administration) or CE (European Union Certification) standards.
6、 Maintenance and testing requirements
1. Regular cleaning
During operation, regularly purge the pipeline with high-purity nitrogen to remove any potential impurities that may have accumulated. Perform degreasing retesting (such as oil residue testing) every 1-2 years.
2. Status monitoring
Install pressure sensors and temperature sensors to monitor the real-time operation status of pipelines and avoid material performance degradation caused by overpressure or high temperature.
summarize
The use of degreased stainless steel pipes for medical oxygen pipelines requires full process control from material, degreasing process, welding and installation to certification testing. The core goal is to ensure oxygen purity (≥ 99.5%), prevent safety risks caused by grease, and meet the hygiene standards of the medical industry. Any negligence in any link may lead to oxygen pollution or safety accidents, so it is necessary to strictly follow relevant regulations (such as the Chinese "Technical Specification for Medical Gas Engineering" GB 50751).
Tags: High purity stainless steel material, Corrosion and oxidation resistance performance, Gas purity guarantee