-
Laijing Bu
Hi there! Welcome to my shop. Let me know if you have any questions.
Your message has exceeded the limit.

The cleaning and disinfection methods for stainless steel pipe oxygen pipelines
2025-07-15 14:20:33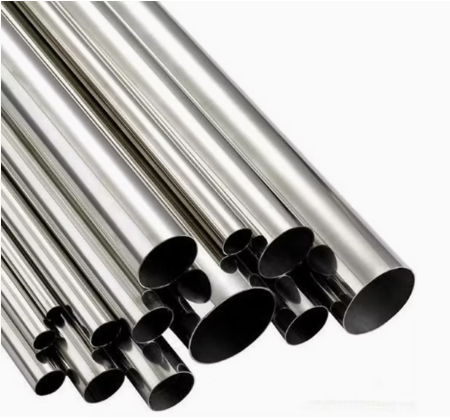
The cleaning and disinfection of medical stainless steel oxygen pipelines are crucial steps to ensure the safety of oxygen delivery and prevent contamination. The appropriate methods should be selected based on the pipeline's usage, contamination level, and hygiene standards. The following is the specific operation process and technical requirements:
I. Core Objectives of Cleaning and Disinfection
Remove impurities:, metal debris, dust, welding slag, etc. (physical contaminants).
Control microorganisms: bacteria, fungi, viruses, etc. (biological contamination), to prevent the oxygen from being contaminated by pathogens.
Eliminate safety hazards: Prevent the contact between oil and oxygen, which may cause combustion or explosion, and reduce the risk of static electricity accumulation on the inner surface of the pipeline.
II. Preparations before Cleaning
1. Pipeline system inspection
Confirm that the pipeline is leak-free, has no mechanical damage, and that the welding points have no burrs or pores (through visual inspection or non-destructive testing).
Remove valves, instruments, etc. from the pipeline (components that cannot be removed need to be isolated with blind plates) to avoid residual cleaning solutions.
2. Tools and reagents preparation
Cleaning tools: dedicated pipeline brushes, sponge balls, high-pressure water guns, pneumatic cleaning equipment, etc.
Cleaning agents:
Decontaminating agent: carbon tetrachloride (CCl₄), trichloroethylene (C₂HCl₃), ethanol (medical grade), etc., which must meet the "oil-free" requirements in GB 50751.
Neutral detergent: pH 6-8 non-phosphorus detergent, used to remove water-soluble dirt.
Disinfectants:
Chemical disinfectants: 3% hydrogen peroxide (H₂O₂), 0.1% peracetic acid, 75% ethanol, sodium hypochlorite (effective chlorine content 500-1000mg/L).
Physical disinfection: high-temperature steam (121℃, 30 minutes), ultraviolet (wavelength 254nm, irradiation time ≥30 minutes).
III. Cleaning Process and Methods
1. Mechanical cleaning (removal of physical impurities)
Step 1: Pre-rinse with clean water (such as purified water, injection water) at a flow rate of 0.5-1m/s for 10-15 minutes to remove surface dust and debris.
Step 2: Decontamination (key step)
Soaking method: Pour decontaminating agent into the pipeline and keep the liquid level submerged in the pipeline. Soak for 30-60 minutes (better effect at 20-40℃). Suitable for short pipes or detachable pipelines.
Circulation method: Use a pump to circulate the decontaminating agent at a flow rate of 1-2m/s to wash the pipeline. Continue for 2-4 hours, suitable for long-distance pipeline systems (such as main trunk lines for central oxygen supply).
Note: The decontaminating agent must be "medical grade oil-free", and it must be thoroughly removed (can be rinsed with ethanol or clean water until no residue is left), to avoid contact between the decontaminating agent and oxygen, which may be dangerous.
Step 3: Mechanical scrubbing
For pipelines with a diameter of ≥DN25, use a pipeline brush dipped in neutral detergent and scrub the inner wall electrically or pneumatically, combined with sponge balls for wiping, to remove stubborn stains and welding slag.
Step 4: Secondary rinsing
Rinse the pipeline with clean water at a flow rate of 1-2m/s until the conductivity of the water is ≤10μS/cm (or meets the medical water quality standards), ensuring that the residual cleaning agent content is <0.1%.
2. Disinfection treatment (control of biological contamination)
Chemical disinfection method
Hydrogen peroxide / peracetic acid disinfection
Prepare 3% hydrogen peroxide or 0.1% peracetic acid solution and pass it through the pipeline at a flow rate of 0.5-1m/s, maintaining contact time of 30-60 minutes, then rinse with sterile water to neutral pH.
Advantage: No residue, decomposition products are water and oxygen, suitable for medical scenarios.
Sodium hypochlorite disinfection
Prepare a solution with an effective chlorine concentration of 500-1000 mg/L. Let it circulate for 30 minutes, then rinse with sterile water until the residual chlorine content is less than 0.5 mg/L. Avoid corrosion of stainless steel by chlorine ions (the concentration and time need to be controlled).
Ethanol disinfection
Dip or wipe the pipes with a 75% ethanol solution, allowing it to act for 15-30 minutes. This method is suitable for short pipes or local disinfection. Be cautious about fire prevention (ethanol is flammable).
Physical disinfection method
High-temperature steam disinfection
Introduce saturated steam at 121℃ with a pressure of 0.1 MPa for 30 minutes. This method is suitable for pipe systems that can withstand high temperatures (it is necessary to confirm the high-temperature resistance of the pipe material).
Ultraviolet disinfection
Install ultraviolet sterilizers in the pipeline system, ensuring the ultraviolet wavelength is 254nm and the irradiation dose is ≥ 40mJ/cm². This is suitable for maintaining disinfection of long-term running pipelines (it needs to be used in combination with chemical disinfection on a regular basis).
IV. Verification and Preservation of Cleaned and Disinfected Surfaces
1. Effect Verification
Visual Inspection: The inner walls of the pipeline should be free of oil stains, rust, and debris, presenting a metallic luster.
Residue Testing:
Oil Residue: Shine the ultraviolet light on the inner walls of the pipeline, and there should be no fluorescence reaction (oil fluoresces under ultraviolet light).
Cleaning Agent Residue: Take water samples for conductivity and pH value testing, or use test strips for testing.
Microbial Testing:
Sampling Method: Use sterile cotton swabs to wipe the inner walls, or take water samples for colony count (for medical oxygen pipelines, the total number of colonies should be ≤ 100 CFU/m²).
Safety Test: After disinfection, an air pressure test (0.6 - 1.0 MPa) needs to be conducted to ensure no leakage.
2. Sealing and Installation
After cleaning and disinfection, the pipeline ports need to be sealed with plastic blind plates or dust covers to prevent dust and moisture from entering. During installation, sterile gloves without powder should be worn. Direct contact with the inner wall is prohibited. If the installation is not completed within 48 hours, the pipeline needs to be cleaned and disinfected again.
V. Notes and Safety Regulations
1. Personal Protection
When handling degreasing agents and disinfectants, wear chemical-resistant gloves and goggles. Work in a well-ventilated environment (for example, avoid inhaling carbon tetrachloride as it is toxic).
2. Material Compatibility
Avoid using cleaners containing chloride ions (such as hydrochloric acid) to prevent stress corrosion of stainless steel (316L has better resistance to chloride ions than 304L).
3. Cycle Management
Before installing new pipelines, the entire process must be thoroughly cleaned and disinfected; for in-use pipelines, regular disinfection is required every 1-2 years (adjust according to usage frequency and contamination risk). If you detect an oxygen odor or microbial, immediately reprocess.
4. Record Keeping
Keep records of the batch numbers of cleaning and disinfectant reagents, operation times, and test results, in accordance with GMP (Good Manufacturing Practice for Pharmaceuticals) or hospital infection control standards.
VI. Relevant Standards and Specifications Reference
GB 50751 "Technical Specifications for Medical Gas Engineering"
YY/T 0801 "Seamless Metal Pipes for Medical Gases and Vacuum Use"
ISO 11135 "Sterilization of Medical Health Products - Ethylene Oxide" (Some disinfection methods are referenced)
"Management Specifications for Hospital Disinfection Supply Centers" (WS 310.1-2016)
Summary
Tags: Cold facts about stainless steel pipes