Home > Blog > What is the difference in the application of 304 and 316L stainless steel materials in the pharmaceu
-
Laijing Bu
Hi there! Welcome to my shop. Let me know if you have any questions.
Your message has exceeded the limit.

What is the difference in the application of 304 and 316L stainless steel materials in the pharmaceu
2025-07-15 09:19:16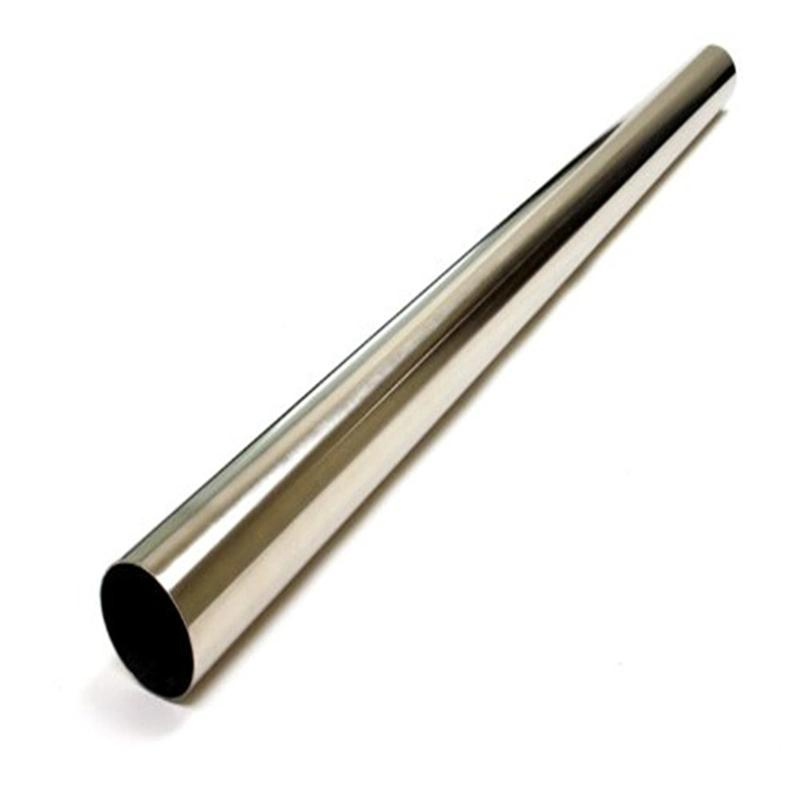
In the pharmaceutical industry, there are significant differences in the application scenarios of 304 and 316L stainless steel due to differences in chemical composition and performance. The following comparative analysis is conducted based on material characteristics, corrosion resistance, compliance requirements, and specific application scenarios:
1、 Differences in chemical composition and core performance
Picture 1
2、 Differences in Corrosion Resistance and Adaptability to Pharmaceutical Scenarios
1. 304 stainless steel: suitable for non chloride ion corrosive environments
Advantages:
It has certain corrosion resistance to conventional acid and alkali (such as dilute solutions of hydrochloric acid and sodium hydroxide), ethanol and other organic solvents, and the cost is relatively low.
Limitations:
It does not contain molybdenum element and is prone to pitting or crevice corrosion in chloride containing media (such as physiological saline and trace chloride ions in purified water). Long term use may lead to pipeline leakage or metal ion contamination of drugs.
Typical applications:
Ordinary purified water (PW) delivery system (chloride ion content ≤ 0.2ppm).
Non corrosive drug solutions (such as oral formulation solutions) are transported through pipelines.
Ventilation and air conditioning condensate pipes in non sterile areas (not in contact with drugs).
2. 316L stainless steel: suitable for high corrosion or sterile environments
Advantages:
Containing molybdenum element, its corrosion resistance to chloride ions (such as chloride ions in WFI injection water ≤ 0.2ppm), sulfur-containing media (such as sodium sulfide solution), and high-temperature steam is significantly better than that of 304.
The ultra-low carbon content prevents intergranular corrosion without the need for additional heat treatment after welding, making it suitable for frequent welding of pipeline systems.
Typical applications:
Water for injection (WFI) system: Directly in contact with sterile drug solutions, it needs to withstand high temperature steam sterilization (121 ℃) and chloride ion erosion.
Pure steam pipeline: Transport pure steam used for sterilization to avoid contamination of drugs with metal ions carried in the steam (in accordance with ASME BPE standards).
Aseptic preparation production line: The connecting pipelines of freeze-drying machines and mixing tanks need to withstand online sterilization (SIP) and chemical disinfectants (such as hydrogen peroxide).
Transport pipelines for chloride ion containing drugs, such as sodium chloride injection and cephalosporin antibiotic solutions.
3、 Comparison of Compliance and Certification Requirements
1. 304 Stainless Steel: Basic Compliance Scenarios
Applicable standards:
Meet the requirements of FDA 21 CFR Part 177.2400 for general food contact materials.
Suitable for non sterile preparations or low-risk areas (such as D-level clean areas), it is required to meet GMP requirements for material traceability (provide COA material certificate).
Limitations:
Not recommended for direct contact with sterile drugs or high-purity media (such as WFI) as it may not pass USP Class VI biocompatibility testing.
2. 316L stainless steel: high compliance scenarios
Compulsory authentication:
USP Class VI certification: Ensure that the material is non-toxic and suitable for direct contact with sterile drugs.
ASME BPE certification: In biopharmaceutical equipment, pipelines must meet the requirements of this standard for surface roughness (Ra ≤ 0.4 μ m) and welding quality.
ISO 10993 biocompatibility testing: avoids contamination of drugs through cytotoxicity and allergenicity testing.
4、 Surface treatment and cleaning requirements
1. 304 stainless steel
Mechanical polishing (MP) is usually used, with an inner surface roughness Ra ≤ 0.8 μ m and an outer surface Ra ≤ 1.6 μ m.
Suitable for systems that can be frequently disassembled and cleaned (such as oral preparation production lines), but long-term use requires attention to passivation treatment of welding areas (such as nitric acid passivation) to prevent corrosion.
2. 316L stainless steel
Priority is given to electrolytic polishing (EP), with an inner surface Ra ≤ 0.4 μ m and a more uniform and dense passivation film on the surface. The corrosion resistance is improved by more than 30% compared to 304.
Suitable for non removable online cleaning (CIP) or online sterilization (SIP) systems (such as sterile formulation pipelines), the smooth surface can reduce bacterial biofilm adhesion.
5、 Special scenario comparison: Taking the injection water system as an example
Picture 2
6、 Summary: How to choose 304 or 316L?
Select scenario 304:
Non sterile, non chloride ion medium, low-risk areas (such as ordinary purified water, oral medication), and limited budget.
The scene where 316L must be selected:
Contact with sterile drugs, injection water, and chloride containing ion media (such as physiological saline).
Frequent sterilization (SIP/CIP) or exposure to highly corrosive environments (such as acidic drugs, disinfectants) is required.
A sterile preparation production line that meets strict regulatory requirements such as FDA and GMP.
Core principle: 316L has become the preferred choice for core scenarios in the pharmaceutical industry due to its advantages in corrosion resistance and compliance; 304 is only used as a low-cost auxiliary material for non critical processes, but its usage scope needs to be strictly controlled to avoid pollution risks.
Tags: Differences in chemical composition and core performance, Differences in Corrosion Resistance and Adaptability to Pharmaceutical Scenarios, Comparison of Compliance and Certification Requirements