Home > Blog > What are the specific requirements for hygiene grade stainless steel pipe materials in the pharmaceu
-
Laijing Bu
Hi there! Welcome to my shop. Let me know if you have any questions.
Your message has exceeded the limit.

What are the specific requirements for hygiene grade stainless steel pipe materials in the pharmaceu
2025-07-15 09:23:31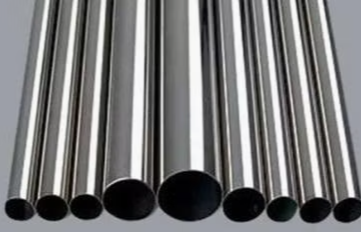
The pharmaceutical industry has extremely strict material requirements for sanitary grade stainless steel pipes, which must meet core requirements such as pollution-free, corrosion-resistant, easy to clean, and comply with Good Manufacturing Practice (GMP) for drug production. The following provides a detailed explanation from the aspects of material characteristics, standard compliance, performance requirements, etc.:
1、 Chemical composition requirements: strict control of impurities and alloying elements
1. Mainstream stainless steel grades and composition restrictions
The commonly used grades in the pharmaceutical industry are 304 (06Cr19Ni10) and 316L (022Cr17Ni12Mo2), and their chemical composition must meet the following key indicators (taking ASTM A270 standard as an example):
Picture 1
2. Impurity control
The use of recycled waste is prohibited, and raw materials must be pure to avoid residual heavy metals such as lead (Pb) and cadmium (Cd), and to prevent drug contamination.
The silicon (Si) content is usually ≤ 1.0% to avoid affecting the surface polishing effect.
2、 Mechanical properties and processing adaptability
1. Strength and ductility
Tensile strength: ≥ 515 MPa (304/316L), yield strength: ≥ 205 MPa, ensuring that the pipeline is not easily deformed or cracked during installation (such as bending or welding).
Elongation rate: ≥ 30%, ensuring the machinability of the pipe (such as cold bending and expansion), and avoiding the generation of microcracks during the processing (cracks are prone to accumulate dirt and grime).
2. Welding performance
Inert gas shielded welding (such as TIG welding) should be used, and the material should meet the requirements of no defects such as porosity, slag inclusion, and incomplete fusion after welding. Passivation treatment (such as nitric acid passivation) should be carried out after welding to restore the passivation film in the welding area and prevent corrosion.
316L has a lower carbon content and a much lower risk of intergranular corrosion after welding compared to 304, making it more suitable for frequent welding scenarios such as pipeline system modifications.
3、 Corrosion resistance: adapting to multiple challenges in pharmaceutical environments
1. Chemical corrosion resistance
Can tolerate acid/alkali solutions (such as hydrochloric acid, sodium hydroxide), organic solvents (ethanol, acetone), and disinfectants (hydrogen peroxide, ozone) during the pharmaceutical process.
316L has significantly better corrosion resistance to chloride containing media (such as physiological saline and purified water) than 304 due to its molybdenum content, and is commonly used in water for injection (WFI) systems.
2. Resistance to intergranular corrosion
It is necessary to use ASTM A262 E method (oxalic acid etching test) or ASTM A262 C method (sulfuric acid copper sulfate test) to ensure that the material does not precipitate chromium carbide at grain boundaries at the sensitization temperature (450-850 ℃), in order to avoid pipeline leakage or contamination caused by intergranular corrosion.
3. High temperature resistance and steam corrosion resistance
Can withstand high-pressure steam sterilization (SIP) at 121 ℃, the material does not oxidize or peel at high temperatures, and there is no metal ion precipitation (such as iron ion contamination of drugs).
4、 Surface treatment and hygiene characteristics
1. Surface roughness (Ra value)
The inner surface roughness should be ≤ 0.8 μ m (ideal value ≤ 0.4 μ m), and the outer surface roughness should be ≤ 1.6 μ m. A smooth surface can reduce bacterial biofilm adhesion (such as FDA requirements for drug contact surfaces to be "crack free and depression free").
It is usually necessary to improve the surface smoothness through electrolytic polishing (EP). After EP, a more uniform passivation film is formed on the surface, and the corrosion resistance is increased by more than 30% compared to mechanical polishing (MP).
2. No porosity and adsorption
The material should be dense and pore free to avoid residual drugs or cleaning agents; The surface must not adsorb organic matter and must pass the "water contact angle test" (contact angle ≥ 60 ° to ensure surface hydrophilicity and facilitate cleaning).
5、 Compliance and Certification Standards
1. International and industry standards
FDA (US Food and Drug Administration): Complies with 21 CFR Part 177.2400 to ensure that there is no migration when the material comes into contact with the drug.
GMP (Good Manufacturing Practice): Material traceability is required, and a Certificate of Material (COA) must be provided for each batch of pipes, including chemical composition, mechanical properties, and surface treatment reports. ISO 14644 (Cleanroom Standard)
Pipes suitable for Class A clean areas (sterile production environments) must pass surface particle testing (≤ 0.5 μ m particle count ≤ 3520/m ³).
2. Biocompatibility certification
Pipelines that come into direct contact with drugs must comply with USP Class VI (United States Pharmacopeia Class VI) or ISO 10993 (Biological Evaluation of Medical Devices), and pass tests for cytotoxicity, allergenicity, irritation, etc. to ensure no biological toxicity.
6、 Additional requirements for special scenarios
1. Pure steam system
316L material must be used and certified by ASME BPE (Biological Processing Equipment Standard) to prevent contamination of drugs with metal ions carried in steam.
2. Production of sterile preparations
The pipe material should be able to withstand online sterilization (SIP) and chemical sterilization (such as formaldehyde fumigation), and the material should not undergo performance degradation (such as passivation film detachment) after repeated sterilization.
3. High purity medium transportation
When transporting injection water (WFI) and purified water (PW), it is necessary to control the total organic carbon (TOC) in the material to be ≤ 500ppb and the dissolved substances to be ≤ 0.5ppm to avoid water pollution.
7、 Comparison of Material Selection and Application Scenarios
Picture 2
summarize
The pharmaceutical industry's material requirements for sanitary grade stainless steel pipes are centered around "safety, non pollution, and traceability". From chemical composition, mechanical properties to surface treatment, strict standards must be met to ensure that impurities are not introduced and corrosion does not occur during the drug production process, while also complying with the compliance requirements of global regulatory agencies. 316L has become the preferred choice for sterile formulations and high-purity media transportation due to its excellent corrosion resistance, while 304 is suitable for routine scenarios with weaker corrosiveness.
Tags: Chemical composition requirements, Mechanical properties and processing adaptability, Corrosion resistance