Home > Blog > How to avoid polishing damage to the surface passivation film of stainless steel pipes
-
Laijing Bu
Hi there! Welcome to my shop. Let me know if you have any questions.
Your message has exceeded the limit.

How to avoid polishing damage to the surface passivation film of stainless steel pipes
2025-07-15 13:59:37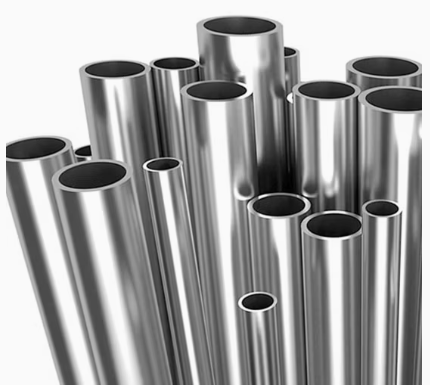
To avoid polishing and damaging the surface passivation film of stainless steel pipes, the following measures can be taken:
Reasonable selection of mechanical polishing parameters
Select suitable abrasives: Choose abrasives with appropriate particle size based on the material and initial surface condition of the stainless steel pipe. For stainless steel pipes with high roughness requirements, coarse-grained abrasives can be used for rough polishing to remove larger machining marks, and then gradually replaced with fine-grained abrasives for fine polishing, such as transitioning from 80 mesh, 120 mesh, to 800 mesh, 1200 mesh or even finer, to avoid excessive damage to the passivation film caused by coarse abrasives.
Control polishing pressure and speed: During polishing, excessive pressure should be avoided, and the pressure should generally be controlled at 1-3kg/cm ². At the same time, the speed of the polishing machine should be adjusted reasonably according to the diameter and length of the stainless steel pipe. For smaller diameter stainless steel pipes, the speed can be slightly higher, such as 2000-3000r/min, while for larger diameter pipes, the speed should be controlled at 1000-2000r/min to prevent damage to the passivation film due to excessive pressure and speed.
Optimize the electrolytic polishing process
Accurate electrolyte preparation: Strictly follow the process requirements to accurately prepare the electrolyte components. For example, for commonly used phosphoric acid sulfuric acid electrolytes, the ratio of phosphoric acid, sulfuric acid, and water is usually controlled between 60% -70%, 20% -30%, and 10% -20%. Some additives such as corrosion inhibitors and brighteners can be added appropriately according to the material of the stainless steel tube and polishing requirements to improve the polishing effect and protect the passivation film.
Strictly control electrolysis parameters: accurately control the temperature and current density of electrolytic polishing. Generally, the temperature is controlled between 40-60 ℃, and the current density is controlled between 15-30A/dm ² according to the material and surface area of the stainless steel tube. At the same time, the electrolysis time should be set reasonably, usually 5-15 minutes, to avoid excessive dissolution of the stainless steel tube surface and damage to the passivation film due to improper temperature, current density, and time.
Adopting a gentle polishing method
Choose chemical polishing: For some stainless steel pipes that do not require extremely high surface quality and have complex shapes, chemical polishing can be used. Chemical polishing can dissolve the micro protrusions on the surface of stainless steel pipes to a certain extent, making the surface smooth, while causing relatively less damage to the passivation film. For example, using a chemical polishing solution containing nitric acid, phosphoric acid, and acetic acid for polishing under appropriate temperature and time conditions can achieve good polishing results and protect the passivation film.
Try magnetic polishing: Magnetic polishing is a method that uses magnetic field force to drive magnetic abrasive to polish the surface of stainless steel pipes. This method has uniform polishing force, minimal damage to the surface of stainless steel pipes, and can effectively avoid excessive damage to the passivation film. It is especially suitable for polishing small-sized and precision stainless steel pipes.
In addition, regardless of the polishing method, cleaning and passivation treatment should be carried out in a timely manner after polishing to restore and enhance the passivation film on the surface of stainless steel pipes and improve their corrosion resistance.
Tags: Reasonable selection of mechanical polishing parameters, Optimize the electrolytic polishing process, Adopting a gentle polishing method