-
Laijing Bu
Hi there! Welcome to my shop. Let me know if you have any questions.
Your message has exceeded the limit.

Comparison of the corrosion resistance of INCONEL alloy 625 and 725
2025-07-15 14:15:49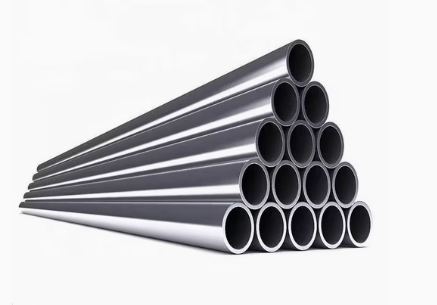
The INCONEL alloys 625 and 725 both have excellent corrosion resistance. They perform similarly in most corrosive environments. However, due to minor differences in composition, their corrosion resistance varies slightly in some specific conditions. Here is the detailed comparison:
Similar corrosion resistance: Both contain a large amount of nickel and chromium. The high content of nickel enables the alloy to have good resistance to corrosion by reducing media, while chromium can form a dense oxide film on the surface of the alloy, enhancing its resistance to oxidative media corrosion. Therefore, they both can provide corrosion resistance in both reducing and oxidizing environments, and both have good resistance to pitting and crevice corrosion, as well as resistance to chloride-ion stress corrosion cracking.
Differences in corrosion resistance in acidic solutions: The INCONEL 625 and 725 alloys have certain corrosion resistance in non-oxidizing acids such as sulfuric acid, hydrochloric acid, and phosphoric acid. At room temperature, both have good corrosion resistance in hydrochloric acid, but as the temperature increases, the corrosion resistance will decrease, and neither is as good as nickel-molybdenum alloys. In phosphoric acid, both have good corrosion resistance, especially for wet-process phosphoric acid environments. However, since the 725 alloy has reduced carbon content and added titanium and aluminum, its sensitivity to carbide precipitation is lower, and in some acidic environments with higher requirements for intergranular corrosion resistance, the corrosion resistance of 725 alloy is slightly better than that of 625 alloy.
Differences in corrosion resistance in specific media: INCONEL alloy 725 exhibits outstanding resistance to corrosion, hydrogen embrittlement, and stress corrosion cracking in oil and gas media containing carbon dioxide, chloride, and hydrogen sulfide. Its corrosion resistance is particularly prominent in deep wells with acidic media, and it is commonly used in downhole tools and wellhead equipment in oil and gas extraction. Although alloy 625 can also withstand these media, when high strength is required while also needing to resist corrosion by such media, alloy 725 is more suitable.
Differences in corrosion resistance under high temperatures: The 625 alloy, due to its solid solution strengthening property, can maintain good corrosion resistance under high-temperature conditions and can be used for a long time in environments above 800℃. It is commonly used in high-temperature components such as gas turbine combustion chambers and aircraft engine exhaust pipes. The 725 alloy mainly enhances its strength through precipitation hardening. Above 650℃, its strengthening phase may decompose, resulting in a decrease in strength and corrosion resistance. Therefore, its operating temperature is generally not more than 650℃.
The following is a comparison chart of the corrosion resistance of INCONEL® alloy 625 and 725. Based on the composition characteristics and environmental adaptability, it is elaborated from four dimensions: corrosion types, typical media, performance differences, and mechanism analysis.
Summary of Key Differences
Intergranular corrosion: 725 significantly outperforms 625 with a low C+Ti/Al ratio, making it suitable for direct use after welding.
Hydrogen sulfide environment: The 725 formulation's enhanced precipitation resistance combined with corrosion-resistant components makes it more reliable in H₂S/CO₂ gas environments.
High-temperature oxidation: The solid solution strengthening mechanism of 625 makes it more stable for long-term use at temperatures above 800℃.
Hydrogen embrittlement susceptibility: The low hydrogen diffusion rate of 625 offers a greater advantage in a strongly reducing environment.
Application Scenario Suggestions
Priority selection 625: High-temperature oxidative environment (such as in gas turbines), strong reducing acids (such as hydrochloric acid), complex welding structures.
Priority selection 725: Medium-temperature and high-pressure oil and gas extraction (in H₂S/CO₂ environment), deep-sea pipelines, high-strength corrosion-resistant fasteners.
Through the coordinated optimization of component design and strengthening mechanisms, the two alloys achieve complementary corrosion resistance properties. Therefore, the most suitable solution should be selected based on the specific working conditions.
Tags: Knowledge about stainless steel