Home > Blog > Introduce the manufacturing process of bright annealing stainless steel seamless pipes
-
Laijing Bu
Hi there! Welcome to my shop. Let me know if you have any questions.
Your message has exceeded the limit.

Introduce the manufacturing process of bright annealing stainless steel seamless pipes
2025-07-18 13:56:40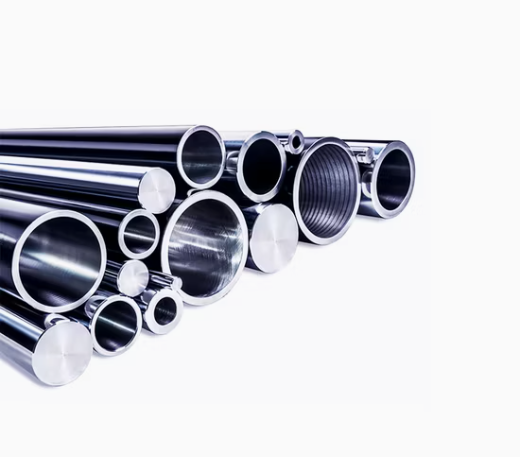
The manufacturing process of bright annealing stainless steel seamless pipes needs to take into account the characteristics of stainless steel and the requirements of the annealing process. It achieves the dual improvement of pipe performance and surface quality through multiple processes. The following is the core process flow and key control points of it:
I. Raw Material Preparation
1. Material Selection
Steel Type: Commonly used austenitic (304/304L, 316/316L), ferritic (430), duplex stainless steel (2205), etc. The choice should be based on corrosion resistance, strength, etc.
Raw Material Form:
Round Steel (Hot Rolling / Forging): Used for piercing process, with diameters typically ranging from φ50 to φ300mm. Sulfur and phosphorus impurities (S ≤ 0.03%, P ≤ 0.035%) need to be controlled.
Continuous Casting Tube Billets: High-precision billets can reduce subsequent processing volume, but attention should be paid to defects such as center porosity.
2. Raw Material Pre-treatment
Surface Cleaning: Remove oxide scale (sandblasting, acid washing) to avoid impurities embedding into the pipe material during piercing.
Heating: Before piercing, the raw material needs to be heated to 1100~1250℃ (for austenitic stainless steel) to ensure good plasticity of the steel billet.
II. Piercing Forming (Foundation Process of Hot-Rolled Seamless Tubes)
1. Types of Piercing Machines
Two-roll inclined rolling piercing machine: The most commonly used type. It uses the combination of the rolls and the head to transform round steel into hollow tubes, with an elongation rate of up to 1.8 to 2.5.
Three-roll piercing machine: Suitable for high-alloy steel, reducing surface defects of the tubes.
2. Key Parameters
Head material: Heat-resistant alloy (such as Cr24Ni7Si2), which needs to be replaced regularly to control the surface quality.
Tube size: The wall thickness is usually 2 to 3 times that of the finished tube, with an outer diameter tolerance of ±1.5%.
III. Tube Rolling and Cold Processing (Dimensional Accuracy and Performance Optimization)
1. Hot Rolling Extension (Optional)
Automatic Tube Rolling Machine: Thinens the raw tube and improves uniformity of wall thickness (tolerance ±10% → ±8%).
Continuous Tube Rolling Machine (MPM): Continuously rolls to increase efficiency, suitable for mass production, with wall thickness tolerance of ±5%.
2. Cold Processing (Determining Final Accuracy)
Cold Drawing / Cold Rolling:
Cold Drawing: Reduces diameter and wall thickness through die drawing, deformation amount per pass 15% - 30%, suitable for small-diameter tubes (φ6 - φ150mm).
Cold Rolling: Multi-roll rolling (such as LG rolling machine), higher precision (wall thickness tolerance ±0.1mm), surface roughness Ra ≤ 1.6μm.
Intermediate Annealing: If the deformation amount exceeds 20% - 30% during cold processing, stress-relieving annealing (300 - 450℃, air cooling) is required to avoid processing hardening and cracking.
IV. Bright Annealing (Core Process)
1. Purpose of Annealing
Structure optimization: Eliminate the deformed martensite and dislocations generated during cold processing, and achieve grain re-crystallization (grain size of 5-8 levels for austenitic steel).
Surface brightening: Suppress oxidation through a protective atmosphere, form a uniform passivation film, and avoid the residue of the oxide layer from traditional annealing.
2. Annealing Equipment and Process Parameters
Furnace type:
Continuous bright annealing furnace: Suitable for mass production, using belt or roller conveyor for transportation, with a furnace length of 20-50m.
Box-type bright annealing furnace: Suitable for small-batch, multi-specification production, with high sealing requirements.
Protective atmosphere:
Hydrogen (H₂): Purity ≥ 99.99%, highly reducing, can reduce the oxide film, commonly used for austenitic stainless steel (such as 304), but be cautious of explosion (hydrogen concentration > 4% is explosive).
Nitrogen-hydrogen mixture gas (N₂ + H₂): H₂ content 5% - 10%, cost reduction while ensuring reducing property, suitable for ferritic stainless steel.
Pure nitrogen gas (N₂): Only used for short-time annealing or scenarios with low surface requirements (such as some ferritic steel).
Temperature and time:
Solution annealing (austenitic steel): 1050 - 1100℃, the holding time is adjusted according to the wall thickness (such as φ50×3mm pipe, holding for 15 - 20 minutes), then rapid cooling (such as water cooling or air cooling), to inhibit the precipitation of carbides.
Re-crystallization annealing (ferritic / martensitic steel): 700 - 900℃, hold for 30 - 60 minutes, air cooling is sufficient, promotes grain homogenization.
3. Key Control Points
Furnace atmosphere dew point: ≤ -40℃ (low dew point to avoid water vapor leading to oxidation).
Heating rate: Cold-worked pipe materials need to be slowly heated (50 - 100℃/h), to prevent stress cracking.
Cooling rate: Austenitic steel needs to be rapidly cooled (cooling rate > 50℃/s), ferritic steel can be slowly cooled.
V. Finishing and Inspection (Ensuring Product Quality)
1. Dimensional Finishing
Straightening: Roll straightening machine eliminates bending (straightness ≤ 1.5mm/m), or tension straightening enhances overall performance.
Cutting: Sawing or fly-cutting with fixed length (length tolerance ±5mm), port grinding to remove burrs.
2. Surface Treatment
Pickling and Passivation (Optional): If there is still slight oxidation on the surface after annealing, clean with nitric acid + hydrofluoric acid solution to form a denser passivation film (increase Cr³+ content).
Polishing: Mechanical polishing (sandpaper / centerless grinding) or electrolytic polishing, roughness can be reduced to Ra ≤ 0.2μm, meeting ultra-high cleanliness requirements (such as in the semiconductor industry).
3. Performance Testing
Mechanical Properties: Tensile test (yield strength, tensile strength, elongation), hardness test (HV/HB).
Corrosion Resistance: Intergranular corrosion test (such as ASTM A262 E method), salt spray test (5% NaCl solution, ≥ 48 hours without corrosion).
Surface Quality: Visual inspection (no cracks, folds, oxidation color), endoscope inspection for internal wall defects.
Dimensional Accuracy: Outer diameter (±0.5%), wall thickness (±5%), straightness (≤1mm/m).
VI. Comparison of Typical Process Routes Picture One
Summary
The manufacturing of bright annealed stainless steel seamless tubes requires balancing the forming accuracy with surface/performance control. The key lies in eliminating cold working stresses through protective atmosphere annealing, refining grains, and ensuring final quality through precise cold processing and inspection. This process is widely used in high-end manufacturing fields. The technical challenges include atmosphere control, temperature uniformity, and the adaptability of the process to different steel types.
#Knowledge about Stainless Steel Pipes# #Knowledge about Seamless Stainless Steel Pipes# #Stainless Steel [Discussion]### Wenzhou · Wenzhou Longwan International Airport [Location]
Tags: Seamless Stainless Steel Pipe, bright annealing, Cold Rolling: