Home > Blog > How to determine whether the thickness of industrial stainless steel pipes meets the standards
-
Laijing Bu
Hi there! Welcome to my shop. Let me know if you have any questions.
Your message has exceeded the limit.

How to determine whether the thickness of industrial stainless steel pipes meets the standards
2025-07-18 13:59:59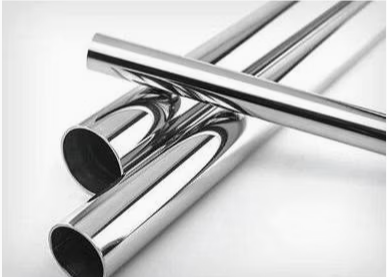
To determine whether the thickness of industrial stainless steel pipes meets the standards, it is necessary to combine the use of measurement tools for inspection, verification of quality documents, and comparison with relevant standards and specifications. The specific methods and operational points are as follows:
I. Direct Measurement Method: Using professional tools to measure wall thickness
1. Ultrasonic thickness gauge (most commonly used)
Principle: The wall thickness is calculated based on the time difference of ultrasonic waves' reflection on the inner and outer walls of the pipe. It is suitable for online or offline detection of seamless pipes and welded pipes, and is particularly suitable for measuring non-ferrous magnetic stainless steel pipes (such as austenitic 304, 316).
Operation steps:
01. Clean the surface of the pipe, remove rust, paint or oxide scale, and expose the metallic luster.
02. Select at least 3 measurement points evenly on the outer surface of the pipe (120° intervals in the circumferential direction, and measure once every 100-200mm along the axial direction).
03. Apply coupling agent (such as glycerin, engine oil), place the probe closely against the surface, and read the stable value. Notes:
If there is corrosion, scaling or coating on the inner wall of the pipe, it may cause measurement errors. It is necessary to clean it in advance or use other methods.
For ferromagnetic stainless steel (such as 410, 430 martensitic steel), a thickness measuring instrument with magnetic permeability compensation should be selected.
2. Micrometer / vernier caliper (suitable for thin-walled pipes or edge measurement)
Micrometer: Accuracy up to 0.001mm, suitable for measuring thin-walled pipes with a wall thickness of ≤ 3mm or the thickness of pipe end ports (samples need to be cut).
Vernier caliper: Accuracy 0.02mm, can measure the outer diameter and inner diameter of the pipe material, and calculate the wall thickness using the formula:
Wall thickness = (outer diameter - inner diameter) / 2
Limitation: It needs to contact the inner and outer surfaces of the pipe material, and is not applicable to long pipes or pipes that cannot be cut.
3. Magnetic thickness measuring instrument (only applicable for coating thickness detection)
Used to measure the coating thickness on the surface of stainless steel pipes (such as galvanized, chrome-plated), it cannot detect the base material wall thickness, and needs to be used in combination with other methods.
II. Quality Document Verification: Traceability of Factory Data
1. Verify the Material Certificate (Quality Assurance Certificate)
Require the supplier to provide the original factory quality assurance certificate, which should include:
Nominal wall thickness (e.g. Sch40, DN50×3.5mm) and allowable tolerance (e.g. ±10% or ±0.2mm, must comply with standard requirements).
Measured wall thickness data: Usually the sampling test results of each batch of pipe materials (e.g. at least 5 measurements per furnace batch).
Compared with standards:
Unfinished tube: As per GB/T 14976-2012 "Fluid Conveyance Stainless Steel Seamless Pipes", the wall thickness tolerance is ±12.5% (ordinary grade) or ±10% (superior grade).
Welded pipe: As per GB/T 12771-2008 "Fluid Conveyance Stainless Steel Welded Pipes", the wall thickness tolerance is ±10%.
2. Review Non-destructive Testing Reports
For high-pressure or critical application pipes, ultrasonic testing (UT) or eddy current testing (ET) should be conducted. The report will indicate whether the wall thickness meets the design requirements.
Key points: Testing ratio (such as 100% testing or sampling testing), handling results of non-conforming areas.
3. Trace Production Process Records
Unfinished tube: Record of hole thickness control during hot rolling / cold drawing process, adjustment parameters of sizing machine.
Welded pipe: Setting of roller spacing in forming unit, wall thickness monitoring data before and after welding.
III. Comparison of Standards and Specifications: Clearly Define the Basis for Qualification Determination
1. Commonly Used Domestic Standards Picture One
2. Qualification determination logic
Single measurement value: The measured value must fall within the specified tolerance range as per the standard (for example, nominal wall thickness 3mm, tolerance ±10%, then the measured value should be ≥2.7mm and ≤3.3mm).
Batch inspection: The sampling pass rate must be ≥95%, otherwise the entire batch of pipe materials needs to be re-inspected or rejected.
Critical areas: Near the weld, bending / tee processing areas may have thinning, so more frequent measurements are required (for example, measure once every 50mm).
IV. Common Causes and Risks of Non-compliance with Thickness Requirements
1. Cause Analysis
Production process issues: During the piercing process of seamless pipes, the gap between the rolling rollers is too large, and the wear of the forming rollers of welded pipes leads to uneven wall thickness.
Cutting corners: Small manufacturers deliberately produce "under-thickness pipes" that are lower than the nominal wall thickness to reduce costs.
Processing losses: During the cold bending and expansion processes of pipe materials, the deformation amount is not controlled properly, resulting in local thinning.
2. Risk Consequences
Insufficient strength: In high-pressure scenarios, it may cause pipeline rupture (such as steam pipeline leakage).
Reduced corrosion resistance: With too thin wall thickness, the medium will accelerate the penetrating corrosion of the pipe material (such as chemical pipeline perforation).
Shortened service life: Under long-term vibration or pressure fluctuations, thin-walled pipes are prone to fatigue cracking.
V. Practical Suggestions
1. Batch Sampling Strategy
For each batch of pipes (same specification, same furnace batch number), at least 2 pipes should be sampled, and 5-10 sections (including both ends and the middle part) should be measured for each pipe.
For pipe fittings such as elbows and reducers, 100% inspection of the wall thickness at the interface is required.
2. Third-party Testing Commissioning
For important projects (such as petrochemicals, pressure vessels), commission a CMA/CNAS certified laboratory for testing to ensure the results are fair and reliable.
3. Clear Contract Clauses
Indicate in the procurement contract: "The pipe wall thickness must comply with GB/T XXX standard, and the measured value must not be lower than 90% of the nominal wall thickness", and stipulate the responsibility for the return and replacement of non-conforming products.
Summary: Flowchart for judgment process Figure 2
#Stainless Steel [Discussion Thread] #Related Knowledge about Stainless Steel Seamless Pipes #Related Knowledge about Stainless Steel Pipes #
Tags: stainless steel pipes, Wall thickness, Clear Contract Clauses