-
Laijing Bu
Hi there! Welcome to my shop. Let me know if you have any questions.
Your message has exceeded the limit.

Different applications of INCONEL alloy 625 and 725
2025-07-15 14:17:03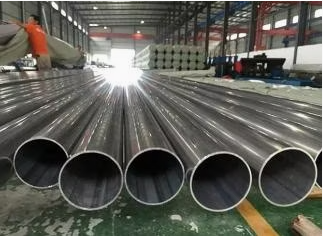
The INCONEL® alloys 625 and 725 differ in composition, strengthening mechanisms, and properties, resulting in distinct application focuses. The core difference lies in the requirements for "high-temperature stability" and "high strength". The following is a detailed description of their specific applications:
I. Typical Applications of INCONEL® 625
625 is mainly characterized by solid solution strengthening and possesses excellent high-temperature stability, corrosion resistance, and machinability. It is mainly used in high-temperature + highly corrosive environments, especially suitable for scenarios that require both "high-temperature strength" and "resistance to complex medium corrosion".
1. Energy and Power Sector
Energy generation: Combustion chambers, transition sections, flame tubes, etc. (required to withstand 800-1000℃ high temperatures and gas corrosion).
Aerospace: Exhaust pipes of engines, turbine outer rings, spacecraft propulsion system pipelines (resistant to high-temperature oxidation and high-speed airflow erosion).
Nuclear power: Heat exchange tubes of nuclear reactors, steam generator pipes (resistant to high-pressure water corrosion and radiation environment).
2. Chemical and Environmental Protection Sector
Chemical equipment: Heat exchangers, reactor linings, agitators (resistant to strong reducing media such as hydrochloric acid and sulfuric acid and high-temperature high-pressure corrosion).
Sulfur dioxide removal: Spray systems of desulfurization towers, absorption pipe systems (resistant to acidic corrosion of sulfur-containing flue gas).
Seawater desalination: Reverse osmosis membrane modules, seawater treatment pump impellers (resistant to point corrosion and crevice corrosion of seawater chloride ions).
3. Other Industrial Scenarios
Marine engineering: Seawater cooling system pipelines, underwater drilling platform connectors (resistant to long-term immersion corrosion in seawater).
Precision instruments: Protective sleeves for high-temperature thermocouples (required to maintain structural stability and corrosion resistance at high temperatures).
II. Typical Applications of INCONEL® 725
725 is based on precipitation hardening and achieves extremely high yield strength (800-1000 MPa) through aging treatment. It is mainly used in medium-temperature (≤ 650°C) and high-pressure environments, and is particularly suitable for scenarios that require "high strength + corrosion resistance" in combination.
1. Oil and Gas Extraction Field
Downhole tools: oil pipes, casing, packers, safety valves (must withstand high pressure in oil and gas wells (over 100 MPa), H₂S/CO₂ corrosion and formation stress).
Wellhead equipment: high-pressure valves, flanges, connectors (resist high-pressure impacts and sulfide stress corrosion in oil and gas extraction).
2. Marine and Deep-sea Engineering
Deep-sea pipelines: joint and fasteners for deepwater oil and gas transportation pipelines (must withstand deep-sea high pressure (increasing by 10 MPa per 100 meters) and seawater corrosion).
Ocean structures: high-strength bolts for platforms, anchor chain connections (balance high load-bearing capacity and seawater corrosion).
3. High-pressure Vessels and Machinery
High-pressure vessels: inner linings and domes of chemical high-pressure reactors (must withstand medium-temperature high-pressure medium corrosion and structural stress).
Precision machinery: heavy-duty bearings, transmission shafts (maintain high strength and wear resistance in medium-temperature environments).
III. The Core Reason for the Differences in Applications
Picture 1
In short, 625 is the "all-rounder for high-temperature corrosion resistance", while 725 is the "specialist in medium-temperature and high-pressure environments". The two have no direct substitution in their respective areas of expertise.
Tags: Cold facts about alloys